Sono stati forniti dal gruppo Bimotor al gruppo Cgm i venti motori “F36” Fpt Industrial destinati a fornire potenza per la costruzione di Fehmarn Belt, il tunnel sottomarino più lungo del Mondo, tra Danimarca e Germania. Unità scelte per l’affidabilità operativa e i livelli di emissioni allineati alle più stringenti normative stage V.
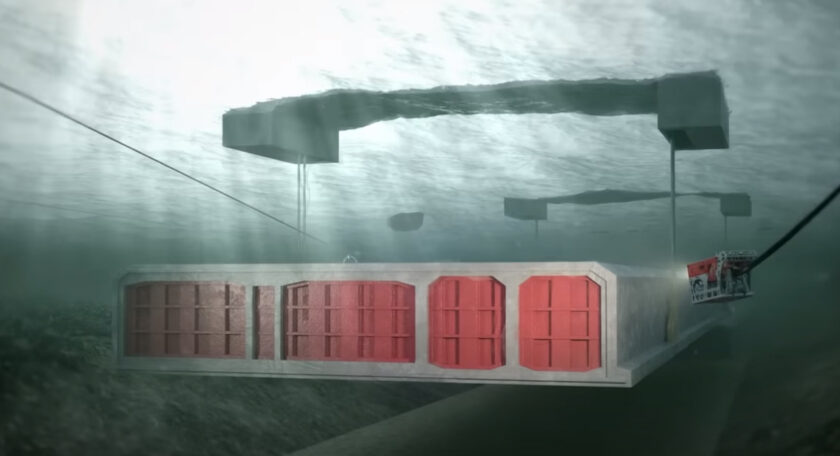
Sono motori Fpt Industrial a supportare la generazione di energia elettrica sul cantiere di Fehmarn Belt, ubicato sullo stretto baltico in essere tra l’isola tedesca di Femern e quella danese di Lolland. Dal 2029 le due isole saranno collegate dal tunnel sottomarino più lungo del Mondo. 18 chilometri che permetteranno di percorrere più velocemente lo stretto di mare potenziando così i collegamenti tra Scandinavia ed Europa Centrale.
Opera alla cui realizzazione sta contribuendo in maniera fattiva anche l’azienda vicentina Cgm, specializzata nella progettazione, realizzazione e assemblaggio di genset per applicazioni industriali professionali. Azienda la cui offerta copre una fascia di potenza che va dai cinque ai tre mila chilovoltampere e che vede a catalogo generatori equipaggiati con unità propulsive di tutti i principali costruttori di motori. Per questo specifico progetto però è stata Fpt Industrial, grazie all’intermediazione del proprio distributore Bimotor, a essere scelta quale fornitore delle unità atte ad azionare i singoli gruppi elettrogeni. I motori serie “F36” da tre litri 594 centimetri cubi di cilindrata sono stati abbinati a generatori in grado di assicurare fino a 100 chilovoltampere di potenza primaria sviluppati a mille 800 giri al minuto.
Prestazioni e sostenibilità
Sono tre le principali motivazioni tecniche che hanno portato Cgm a scegliere “F36” di Fpt Industrial quali unici motori per un progetto così importante. La prima è il livello prestazionale. I gruppi elettrogeni prodotti da Cgm saranno chiamati a sostenere la produzione di corrente durante le operazioni di posa e assemblaggio dei segmenti di tunnel sul fondo del mare. Operazione che richiede differenti lavorazioni dando luogo a carichi estremamente variabili in termini di assorbimenti.
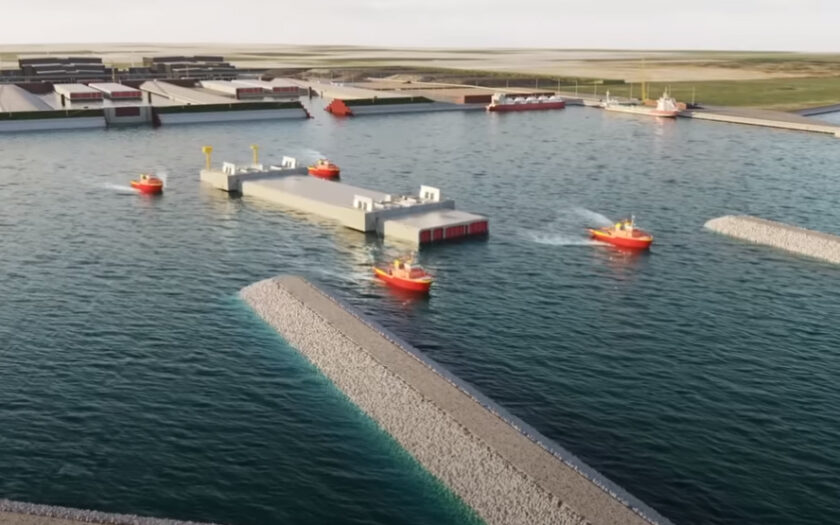
Per questo motivo Cgm ha realizzato quattro generatori contenuti in altrettanti container in ciascuno dei quali operano cinque gruppi elettrogeni in parallelo. Un’architettura che permette di generare fino a due mila chilovoltampere di potenza totale permettendo anche a ciascun motore di entrare in funzione quando le condizioni di carico lo richiedono. Accade quindi che ogni motore lavora nelle condizioni di massima efficienza contribuendo a minimizzare i costi di gestione e la sostenibilità del cantiere. Esigenza quest’ultima che Cgm ha ritenuto basilare e che ha contribuito a guardare verso gli “F36”.
Pochi produttori motoristici offrono infatti all’interno del segmento power generation unità allineate alle più stringenti normative internazionali sulle emissioni. E nessuno può vantare i sistemi di post trattamento dei gas di scarico “Hi-eScr2” di Fpt Industrial. Gruppi pre-assemblati e pre-validati che permettono alle unità di assecondare le normative stage V facilitando l’integrazione dei motori all’interno dei più diversi contesti operativi. Siano essi stazionari o su macchine operatrici semoventi.
Manutenzione ogni 600 ore
Altro motivo alla base della scelta Cgm l’elevata affidabilità e capacità di tenere il carico richiesto anche in condizioni di lavoro difficili. Come quelle del cantiere di Fehmarn Belt. Non a caso Fpt Industrial ha consegnato i motori equipaggiati con un sistema di raffreddamento progettato ad hoc per sopportare gli stress termici ai quali sono sottoposte le unità su cantiere. Soluzione che unita a una predisposizione delle utenze motore su singolo lato, alla presenza di punterie idrauliche e a filtri studiati per minimizzare gli interventi manutentivi permettono alle unità di operare sulla base di intervalli di manutenzione scaglionati ogni 600 ore di lavoro.
Disponibili in tre fasce di potenza, dai 63 ai 90 chilowatt, gli “F36” si distinguono sul mercato per il raggiungimento delle performance operative offerte senza eccedere in stress termici e meccanici. Questo grazie a un dimensionamento bilanciato dell’architettura motore che vede i quattro cilindri in linea sviluppare il volume di tre litri 594 centimetri cubi da canne cilindri da 102 millimetri di alesaggio per 110 millimetri di corsa.
Potenza Fpt per il Fehmarn Belt
Il rapporto corsa alesaggio di otto centesimi sopra l’unità si distingue nel proprio segmento quale parametro più basso grazie alla corsa di soli 110 millimetri. Ne consegue una velocità media del pistone contenuta in poco più di otto metri secondo se calcolato a regime nominale di due mila duecento giri lasciando all’elevata efficienza combustiva, con pressione medie effettive che nella taratura di punta da 105 chilowatt, 143 cavalli, tocca i 21 bar grazie al raggiungimento di coppie massime dell’ordine dei 600 newtonmetro a mille 400 giri al minuto.
Prestazioni raggiunte grazie anche al sistema di alimentazione common rail a controllo elettronico operante a mille 800 bar e un sistema di sovralimentazione con singolo turbocompressore. Il tutto con dimensioni e pesi tra i più contenuti della categoria. Le prime sono contenute all’interno di poco più di tre decimi e mezzo di metro cubo, arrivando con sistema di raffreddamento integrante ventola e radiatore a superare di poco il metro di lunghezza e di altezza, per una larghezza sotto i 700 millimetri. Il peso dell’unità senza impianti ausiliari stalla a 320 chili, attestandosi al limite inferiore della categoria. Peso che con impianto di raffreddamento e sistemi ausiliari non supera i 45 quintali.
73 mila tonnellate a sezione
La costruzione del tunnel di Fehmarn Belt ha richiesto la creazione di uno dei cantieri più grandi d’Europa e la costruzione del più grande sito produttivo di elementi di calcestruzzo del Mondo, comprensivo di un porto dedicato. I 18 chilometri di tunnel infatti saranno realizzati da 89 sezioni prefabbricate integranti cinque condotte affiancate. Due dedicate al traffico veicolare su gomma e due al traffico ferroviario più una quinta di servizio. La struttura di ciascuna sezione, lunga 217 metri, è costituita da un telaio portante di acciaio affogato nel calcestruzzo, soluzione che porta ogni sezione a pesare 73 mila tonnellate.
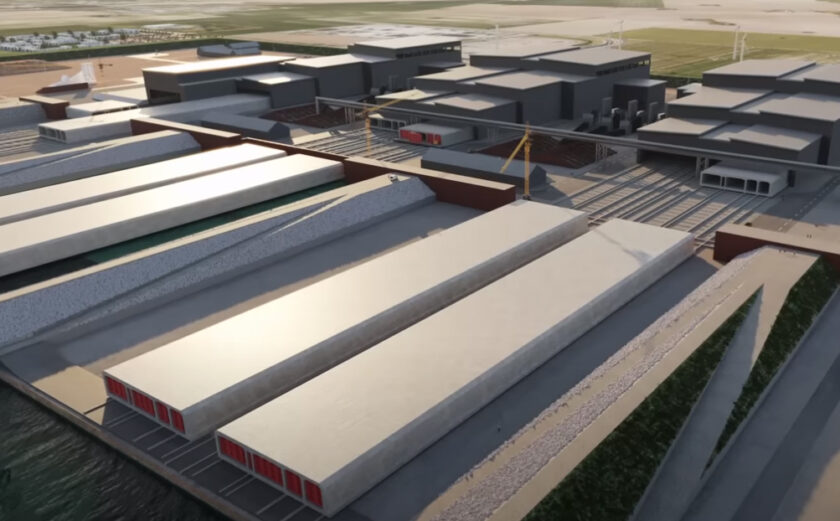
La produzione avviene in una fabbrica dedicata organizzata su sei linee produttive operanti 24 ore al giorno sette giorni su sette che permette di produrre a regime una sezione ogni nove settimane. Usciti dalla fabbrica le sezioni sono fatte scorrere su una rotaia dedicata fino al porto costruito ad hoc dove sono posizionate in un bacino a secco e sigillate a entrambe le estremità. Una volta allagato il bacino le sezioni risultano quindi galleggianti e ciò permette di spostarle via mare fino al punto di posizionamento, lungo una trincea scavata sul fondale marino a 12 metri di profondità.
Apertura nel 2029
Gli elementi vengono quindi affondati e posizionati lungo la trincea con una precisione che prevede uno scarto di 15 millimetri su 15 chilometri di lunghezza. Una volta unite e sigillate tra loro le sezioni sono poi svuotate permettendo di approntare le opere interne di finitura e disposizione degli impianti.
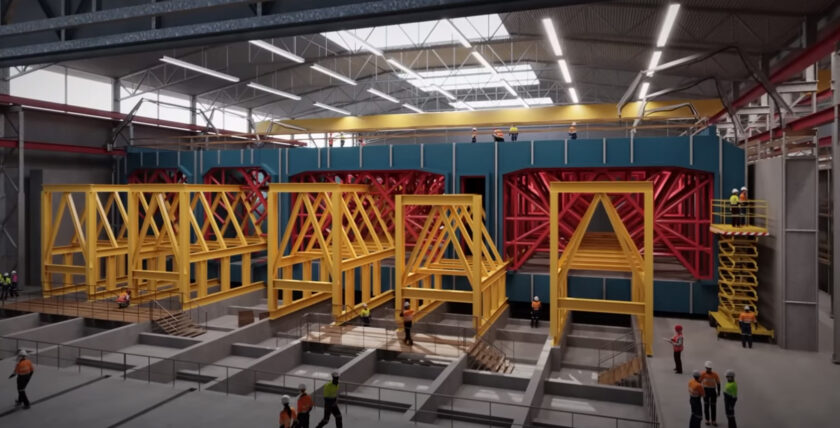
La trincea, una volta ricoperta con terra e rocce, sovrasterà completamente gli elementi del tunnel permettendo il ripristino dell’ecosistema marino. I 19 milioni di metri cubi di terra, sabbia e rocce rimosse per creare la trincea verranno invece riutilizzati per realizzare nuove spiagge e lagune a fianco dell’area di imbocco del tunnel ottimizzando la sostenibilità ambientale dell’opera. Dal 2029 treni e veicoli che collegano le due isole potranno dunque vedere i rispettivi tragitti ridotti anche di 160 chilometri e potranno raggiungere le rispettive mete in sette o dieci minuti a seconda che si tratti di treni o veicoli su gomma.
Potenza Fpt per il Fehmarn Belt
Autore: Jacopo Oldani